Advanced Techniques in Steel Stamping for Precision Production
As sectors constantly require finer resistances and intricate designs in their metal components, the quest for advanced strategies in steel marking has magnified. From the utilization of innovative multi-stage stamping procedures to the combination of sophisticated automation modern technologies, the landscape of steel marking is going through a profound makeover.
Advanced Multi-Stage Stamping Procedures
Talking about the complexities of innovative multi-stage stamping procedures exposes the innovative strategies utilized in modern manufacturing methods. Metal Stamping. Multi-stage marking is a complex procedure that entails multiple actions to change a flat sheet of steel right into a last stamped item. Using progressive dies, where different procedures are done at each phase of the marking procedure, permits high precision and performance in the production of detailed metal components
During the initial stages of multi-stage stamping, the level steel sheet is fed into the marking press, where a series of dies are used to cut and shape the material. Succeeding phases entail added developing, flexing, and punching procedures to further fine-tune the part. Each stage is meticulously created to develop upon the previous one, resulting in the development of complex geometries with limited tolerances.
Advanced multi-stage stamping processes call for a high degree of expertise and precision to ensure the high quality and consistency of the stamped components. By making use of innovative equipment and tooling, makers can generate a vast array of metal elements with efficiency and precision.
Precision Tooling Innovations
Precision tooling innovations have actually reinvented the steel marking industry, improving efficiency and top quality in manufacturing procedures. CNC systems allow for detailed layouts to be equated directly right into tooling, guaranteeing accuracy and repeatability in the marking process.
In addition, the combination of sensing units and real-time monitoring capacities in accuracy tooling has actually made it possible for manufacturers to identify and attend to concerns promptly, reducing downtime and minimizing scrap prices. By including clever technology into tooling, operators can optimize specifications such as stress, speed, and positioning throughout the marking procedure, causing enhanced item top quality and boosted performance.
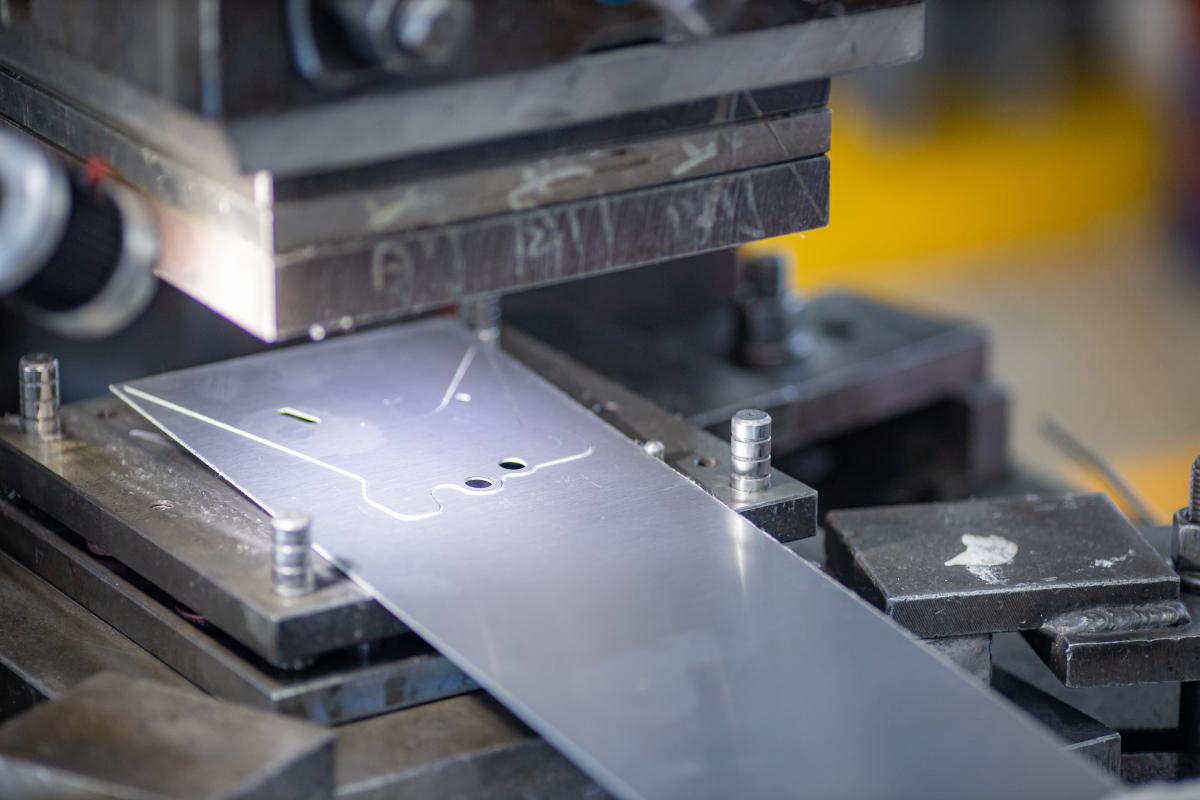
Automation in Metal Stamping
The evolution of precision tooling advancements in the metal marking sector has paved the method for significant innovations in automation, changing the production landscape towards enhanced effectiveness and performance. Metal Stamping. Automation in steel marking entails making use of innovative machinery and robotics to carry out different tasks typically performed by human drivers. This shift in the direction of automation uses various advantages, consisting of enhanced precision, quicker production cycles, and minimized labor expenses
One trick aspect of automation in metal marking is the implementation of computer system mathematical control (CNC) systems, which make it possible for specific control you can look here over the marking procedure. CNC modern technology enables the development of complex and detailed metal get rid of consistent top quality. Additionally, automated systems can be programmed to run continuously, leading to higher outcome prices and shorter lead times.
Additionally, automation improves office safety by reducing hand-operated handling of hefty products and minimizing the danger of accidents (Metal Stamping). As manufacturing sectors continue to embrace automation, the future of metal stamping holds terrific promise for go to the website even higher performance and development
High-Speed Stamping Techniques

Among the main advantages of high-speed stamping methods is the capacity to produce a big quantity of parts in a shorter quantity of time contrasted to standard stamping techniques. This raised productivity not just enables producers to satisfy limited manufacturing deadlines yet also enables cost financial savings via economic situations of range. Furthermore, high-speed marking can help minimize material waste by maximizing the product use during the stamping procedure.
Additionally, high-speed marking methods typically incorporate cutting-edge attributes such as quick die modification systems and real-time monitoring capabilities, better boosting the general performance and adaptability of the metal stamping process. As modern technology remains to advance, high-speed stamping is expected to play a crucial duty in driving the future of precision production.
Top Quality Control in Stamping Procedures
Efficient quality control steps are important for making certain the integrity and consistency of metal marking operations. Quality control in marking procedures includes a series of systematic procedures targeted at spotting and stopping problems in the made components. One essential element of quality assurance in helpful hints steel marking is making use of sophisticated inspection strategies such as optical assessment systems and coordinate measuring makers (CMMs) to verify the dimensions and tolerances of stamped parts.
Additionally, high quality control procedures in marking operations usually consist of the implementation of analytical process control (copyright) methods to monitor the production process in real-time and ensure that it continues to be within acceptable limits. By assessing information and determining fads, suppliers can proactively resolve any type of deviations from the wanted quality requirements.
In addition, top quality control in steel marking procedures also includes extensive product testing to ensure that the raw products utilized satisfy the required specs for the marking process. This may consist of conducting product firmness tests, tensile toughness examinations, and dimensional examinations to guarantee the high quality and honesty of the stamped parts. In general, carrying out durable quality assurance measures is crucial for achieving top notch stamped parts consistently.
Verdict
To conclude, progressed strategies in steel stamping play an essential duty in accuracy production procedures. Through multi-stage marking procedures, ingenious tooling solutions, automation, high-speed methods, and rigorous quality control measures, manufacturers can achieve greater degrees of precision and efficiency in their operations. These innovations in metal stamping innovation have made it possible for business to produce intricate parts with limited resistances, inevitably causing enhanced item high quality and consumer fulfillment in the production market.
Comments on “Why Metal Stamping is Crucial for Developing Durable and Intricate Components”